Core advantages of ultrasonic cutting machine: why is it the preferred choice in the cutting field?
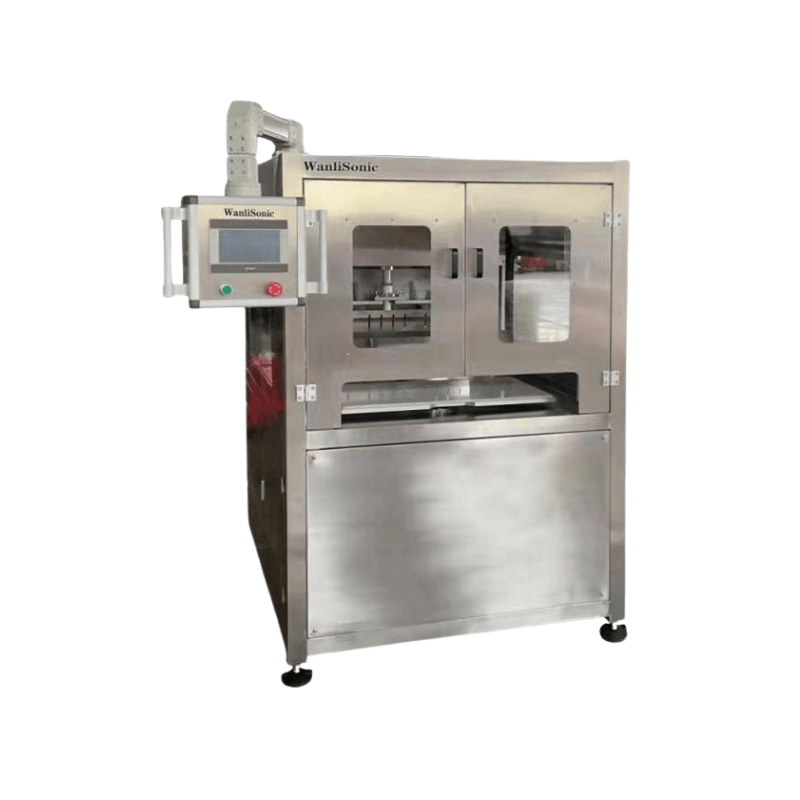
The ultrasonic cutting machine, as an efficient and precision cutting device, its core selling points revolve around cutting quality, application range, operational experience, efficiency, and cost control. Here are the details:
1. Extremely high cutting precision and excellent edge effect
- No burrs or deformation: Ultrasonic cutting uses high-frequency vibration (usually 15-70kHz) to create tiny gaps between the cutting blade and the material, reducing direct friction between the material and the blade. This avoids common issues in traditional cutting such as burrs, curling, and deformation.
- Smooth and flat cuts: It is particularly suitable for soft or sticky materials like plastics, rubber, films, and fabrics. After cutting, no secondary processing is needed, directly meeting high-precision assembly or appearance requirements.
2. Extremely wide range of applicable materials and strong compatibility
Ultrasonic cutting machines break through the limitations of traditional cutting on material hardness and viscosity, and can efficiently handle various special materials Many materials (such as soft, brittle, sticky, and heat-sensitive materials) are extremely sensitive to mechanical force and temperature. Traditional cutting (such as blade extrusion and laser high temperature) is prone to damage, deformation, or performance changes, but ultrasonic cutting can perfectly avoid this problem:
- Soft/elastic materials: Such as silica gel, sponges, foams, leather, and fabrics, avoiding material deformation caused by extrusion.
- Sticky/materials prone to sticking to blades: Such as chocolate, candies, tapes, and hot melt adhesives. High-frequency vibration reduces adhesion between materials and blades, ensuring smooth cutting.
- Brittle/fragile materials: Such as glass fibers, ceramic sheets, and electronic components. Low-pressure cutting reduces the risk of material fragmentation.
- Composite/multi-layer materials: Such as multi-layer fabrics and composite material plates, which can be cut synchronously in multiple layers at one time with high alignment of the cuts.
3. No thermal damage during cutting, protecting material properties
- Low-temperature cutting: Unlike laser cutting or hot knife cutting, ultrasonic cutting mainly relies on mechanical vibration energy, generating minimal heat. It will not cause materials to burn, melt, or discolor due to high temperatures.
- Protection of sensitive materials: It is especially suitable for temperature-sensitive materials such as electronic components (e.g., PCB boards, wires), food (e.g., cakes, cheese), and medical supplies (e.g., gauze, films), ensuring product performance and quality are not affected.
4. Efficient operation, reducing production costs
- Fast cutting speed: High-frequency vibration makes cutting more efficient. Compared with manual cutting or traditional mechanical cutting, it can significantly improve production efficiency, suitable for mass production scenarios.
- Less blade wear: Reduced friction between the blade and the material extends the service life of the blade, lowering the frequency and cost of consumable replacement.
- Strong adaptability to automation: It can be easily integrated into automated production lines, combined with robotic arms, conveyors, etc., to achieve unmanned operation, reducing labor costs and human errors.
5. Low cutting pressure, reducing material loss
- Low-pressure cutting: Only a small amount of pressure is needed to complete the cutting, which is especially suitable for thin materials (e.g., films, sheets) or fragile materials (e.g., foams, paper products), avoiding material stretching, damage, or waste caused by excessive pressure.
- Saving raw materials: High-precision cutting and low-loss characteristics can improve material utilization and reduce the scrap rate in production.
6. Environmentally friendly and safe, improving production environment quality
- No dust or smoke pollution: No high-temperature combustion occurs during cutting, so no dust, smoke, or harmful gases are generated, meeting environmental protection requirements and protecting the health of operators.
- Controllable noise: Compared with the high noise of traditional mechanical cutting, ultrasonic cutting machines operate with lower noise (usually controlled below 80 decibels through sound insulation design), improving the production workshop environment.
In summary, the core advantages of ultrasonic cutting machines lie in high precision, wide compatibility, no thermal damage, and high efficiency, making them irreplaceable in industries with strict requirements for cutting quality and material property protection (such as electronics, food, packaging, medical care, and automobile manufacturing).